Descarbonizando las industrias más contaminantes del mundo
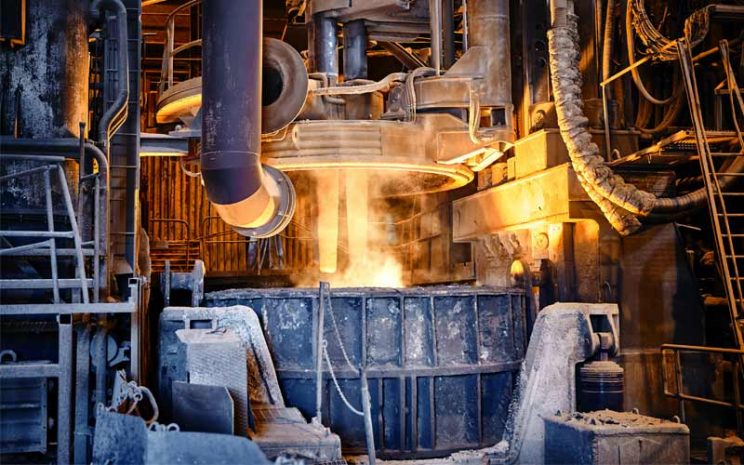
La producción de acero, cemento y energía son las industrias más contaminantes del mundo. El sector energético es responsable del 25% de las emisiones globales de carbono, principalmente por la quema de combustibles fósiles como el carbón, el petróleo y el gas natural. En los EE. UU., el sector eléctrico representa el 30 % de las emisiones totales, mientras que en China representa el 50 %. la industria del cemento, la segunda industria con mayor emisión de carbono después de la energía representa el 8% de las emisiones totales. China, el mayor productor de cemento, es responsable de la mitad de las emisiones mundiales relacionadas con el cemento. La producción de una tonelada de cemento supone la emisión de 0,8 toneladas de CO2. La industria del acero también es una fuente importante de emisiones de gases de efecto invernadero, ya que representa el 25 % de las emisiones directas de GEI de los sectores industriales y el 7 % de las emisiones directas totales.
Reducción de las emisiones de carbono en la producción de energía
Una fuente importante de emisiones de carbono del sector eléctrico son las centrales eléctricas de carbón, que generan alrededor del 35% de la electricidad mundial. El generador de vapor, también conocido como caldera, es un componente importante en una central térmica. Actualizar una central eléctrica a carbón con un generador de vapor supercrítico o ultra supercrítico puede aumentar la eficiencia en un 23 % o un 48 %, respectivamente. Estos generadores de vapor funcionan a temperaturas y presiones más altas, lo que permite que el vapor produzca más energía en la turbina con menos combustible y menos emisiones de carbono. El uso de carbón con bajo contenido de humedad y azufre también puede reducir el uso de combustible y las emisiones de CO2.
La combustión conjunta, el proceso de utilizar gas natural como combustible complementario en una central eléctrica alimentada con carbón, puede ser una forma eficaz de reducir las emisiones de CO2. El alcance de esta reducción depende de la tasa de combustión conjunta, el porcentaje de gas natural en la mezcla de combustible y el rango del carbón. Los desafíos en la combustión conjunta incluyen la necesidad de infraestructura adicional y la posibilidad de inestabilidades en la combustión. Una alternativa es convertir una central eléctrica de carbón en una central de ciclo combinado de gas natural (NGCC), que puede lograr una reducción de hasta un 70% en las emisiones de CO2 en comparación con la mayor intensidad de emisión de las centrales eléctricas de carbón. En una planta NGCC, el calor residual de la turbina de gas se utiliza para generar electricidad adicional en la turbina de vapor, lo que aumenta la eficiencia general de la planta con menores emisiones de carbono.
Reducción de las emisiones de carbono de la industria del cemento
Las materias primas alternativas pueden ayudar a reducir aún más la huella de carbono. Las cenizas volantes y la escoria, que son subproductos de la combustión del carbón y la producción de acero, respectivamente se pueden utilizar como reemplazo parcial del clínker, el componente principal del cemento. La producción de clínker es un proceso que consume mucha energía y es uno de los principales contribuyentes a las emisiones de gases de efecto invernadero en la industria del cemento. En ese sentido, el uso de materiales cementicios alternativos puede ayudar a reducir la demanda de cemento, lo que se traduce en menores emisiones. Ejemplos de tales materiales incluyen ceniza de cáscara de arroz del proceso de molienda de arroz, escoria de alto horno granulada molida y humo de sílice del proceso de producción de aleaciones de ferro silicio. El uso de combustibles alternativos es otro enfoque, en el que las fuentes de energía fósil (carbón y coque de petróleo) pueden sustituirse por combustibles alternativos (p. ej., aceite de desecho, neumáticos, plásticos.)
La implementación de tecnología de eficiencia avanzada puede mejorar la eficiencia de la producción de cemento y reducir los requisitos de energía, lo que se traduce en menores emisiones. Por ejemplo, el uso de tecnología de proceso seco para moler materias primas y formar clínker mediante un proceso seco en lugar de un proceso húmedo puede reducir el consumo de energía hasta en un 40 %. La tecnología de precalentador-precalcinador, que precalienta y precalcina las materias primas antes de introducirlas en el horno, también puede reducir el consumo de energía hasta en un 25 %. Además, es importante considerar los efectos de la carbonatación, la absorción de CO2 atmosférico por parte del cemento durante la construcción, en los inventarios de mitigación de emisiones de CO2. Durante la carbonatación del cemento, el CO2 reacciona con el hidróxido de calcio, un subproducto del proceso de hidratación del cemento, para formar carbonato de calcio.
Reducción de las emisiones de carbono de la industria siderúrgica
La tecnología de fabricación de acero basada en hidrógeno utiliza hidrógeno en lugar de coque para reducir el mineral de hierro a hierro puro, que luego se refina en acero. Este proceso implica la modificación del gas de horno de coque (COG) para aumentar su contenido de hidrógeno para su uso en altos hornos. El COG se produce cuando el carbón se calienta sin oxígeno y se compone principalmente de hidrógeno, metano y monóxido de carbono. Se puede reformar con vapor para producir gas rico en hidrógeno utilizando el calor residual de los hornos de coque. El reformado descompone el metano y otros hidrocarburos en COG a altas temperaturas y presiones para producir hidrógeno y dióxido de carbono. La optimización de las reacciones químicas del horno, la mejora de la calidad del coque, el sinterizado y la escoria, y el uso de tecnologías de transporte cerradas, reductoras de mantenimiento de la temperatura, como las cintas transportadoras tubulares y el transporte neumático, también pueden ayudar a reducir las emisiones en la fabricación de acero.
El potencial de reducción de carbono de la fabricación de acero a base de hidrógeno depende de la fuente de hidrógeno. El hidrógeno verde, producido a partir de fuentes de energía renovables, y el hidrógeno azul, producido a partir de combustibles fósiles utilizando tecnología de captura y almacenamiento de carbono (CCS), son las fuentes más prometedoras. CCS es de alto costo y consume mucha energía, y el costo de capturar carbono de grandes plantas de energía es más bajo que el de fuentes más pequeñas. El costo del hierro y el acero derivados del hidrógeno depende del precio de la energía renovable utilizada para la generación de energía con hidrógeno e hidrógeno. Para que las tecnologías ultra bajas en carbono en la industria del hierro y el acero tengan éxito, el costo de la electricidad debe caer por debajo de los 25 USD/MWh. Existe una oportunidad de inversión en la creación de instalaciones de energía renovable para producir hidrógeno verde, ya que se espera que la demanda de hidrógeno alcance 13-16 Mt por año.
- Columna publicada originalmente en Diario Estrategia el martes 11 de abril de 2023.